Introduction
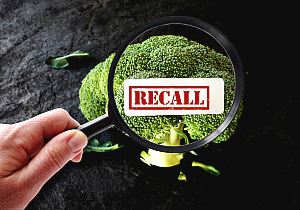
A food recall occurs when there is reason to believe that a food may cause consumers to become ill. A food manufacturer or distributor initiates the recall to take foods off the market. In some situations, food recalls are requested by government agencies (USDA or FDA). Some reasons for recalling food include:
- Discovery of an organism in a product which may make consumers sick.
- Discovery of a potential allergen in a product.
- Mislabeling or misbranding of food.
- Physical hazards found in the food, such as plastic, glass, metal, etc.
There are three classes of food recalls:
Class | Definition | Examples |
---|---|---|
Class I | A health hazard situation where there is a reasonable probability that eating the food will cause serious, adverse health consequences or death. | E. coli O157:H7 in bagged spinach; Salmonella in tomatoes |
Class II | A health hazard situation where there is a remote probability of adverse health consequences from eating the food. | Product containing a foreign material |
Class III | A situation where eating the food will not cause adverse health consequences. | Food product not labeled correctly |
From 2009 to 2013, there was an average of more than 600 food recalls per year in the U.S. food system. This estimate includes both domestic and imported products (USDA ERS, 2018). Food recalls may affect foods used in school meal programs that are distributed by USDA, or a purchased from a commercial source.
School nutrition program staff are responsible for maintaining the safety and security of foods once they are received and stored. Maintaining the chain of custody is also an important responsibility of school nutrition program operators because it allows food products to be traced one step back to the vendor and one step forward to the consumer. In the event of a recall, a food product must be traced to its current location, and schools are to follow the recall procedures outlined in the manufacturer’s instructions or sent by USDA. To respond to recalls of commercially purchased foods, you can be proactive and expedite the process by signing up to receive food recall notifications from the federal government.
If a recall affects a USDA Food, you also can sign up for free email notifications through the Commodity Alert System.
This mock recall resource provides instructions on how to practice conducting a school district-wide recall of fresh produce. Many other produce safety training materials have been developed by USDA FNS. The goal for this activity is to encourage school nutrition program directors to conduct a district-wide mock recall of a fresh produce item that includes the participation of all school site kitchens and fresh produce distributors. Select a fresh produce item, or fresh-cut produce item for this exercise. You can adapt this resource to conduct a mock recall of other types of food, including canned and frozen produce, or any other food.
Conducting an Effective Mock Recall
Through a mock food recall, a school nutrition program can test its response time and identify any weaknesses in the program’s ability to respond to food recalls. Iowa State University Leopold Center for Sustainable Agriculture recommends that growers conduct a timed mock recall annually. The National Restaurant Association Educational Foundation’s ServSafe® training program recommends that restaurant operators test their crisis management plans at least annually. School nutrition program directors should test, on an annual basis, their ability to respond to food recalls and identify areas that need improvement.
A mock recall is a simulated recall exercise with a designated time limit. The amount of time that would be realistic and appropriate varies from school district to school district. School nutrition program directors and/or supervisors should be responsible for setting a realistic target for the amount of time to conduct the mock recall exercise in their district. Examples of factors that might affect response time include district size, amount of produce involved, and type of notification system used.
The following steps outline how to conduct a mock recall of a fresh produce item in a school nutrition operation:
- Step 1 - Review Applicable Standard Operating Procedures (SOPs)
- Review all SOPs that pertain to food recalls. These may address procedures for handling a recall, receiving deliveries, or transporting food between sites.
- Update SOPs, if necessary.
- Communicate updated SOPs to school nutrition staff, if necessary.
- Conduct this step at least one month prior to the planned exercise.
- Step 2 - Review Emergency Notification Contact List
- Create or update the school district’s and school nutrition department’s emergency notification lists to be used in the event of a recall. The lists should include phone numbers and email addresses where staff can be reached both during and after regular work hours.
- Distribute the updated emergency notification contact list to school nutrition program staff at the beginning of the school year, or at any time that staff or contact information changes. In an effort to conduct an unannounced mock recall, distribute the revised emergency contact list at least one month prior to exercise.
- Step 3 - Planning the Mock Recall
All communications should begin with “This is a test.” Begin all phone calls, emails, or anything else in print with “This is a test.”
- Conduct a review during training at the start of the school year, or at least one month prior to the mock recall exercise. During this review, discuss SOPs that address food recalls with all school nutrition staff at the district and school levels and warehouse personnel, if applicable. Any school personnel who have a role during a food recall should be included in the review.
- Determine which produce item will be used in the recall simulation. You may want to include your vendor when making this decision. For fresh produce mock recalls, select a fruit or vegetable that is typically ordered weekly by the school district for use at all school sites, such as salad greens. If seasonal produce is selected, choose a product that will be shipped to all or a majority of schools.
- Identify the date and time that the mock recall will take place within the school district. Although it may be more convenient to conduct a mock recall at certain times because of staff and production schedules, remember that an actual recall could take place at any time of day. By conducting the exercise at unannounced and unpredictable times, you will be able to determine more accurately how long the response might take during an actual recall.
- Set a goal for the amount of time that it should take to identify the locations of all recalled product. Again, the time may vary depending on factors such as district size, day and time of recall, amount of produce affected, and type of communication used in notification.
- Inform school district administrators, including the district’s communications officer and emergency manager, that a mock recall of produce will be conducted. Provide administrators with information on the date(s), time(s), and location(s) of the mock recall exercise. Communicate that the mock recall is only a drill to test the district’s response time and recall procedures, and that produce served to students during the drill is safe to eat.
- Step 4 - Conduct the Mock Recall
- Identify the date and time of the mock recall*. Performing the exercise at unannounced, unpredictable times will result in a more accurate test of the school nutrition program’s recall response capability.
- Place the produce order as usual. Be sure that the vendor knows that “this is a test.”
- Get produce tracking information from the produce vendor including:
- Produce name/description.
- Produce identification numbers (product code, Lot/Batch number, or GTIN, if available) and where they are located on product packaging.
- Produce date(s) (examples: ship date, best if used by, or expiration date).
- Quantities shipped to each school.
- Photograph of labeling containing identification numbers and dates, if possible.
- Record the start time of the mock recall.
- Communicate the produce recall to all necessary personnel at each school site. Follow the SOPs. Be sure to convey that “this is a test.”
- Identify the amount of the produce found at each site. Be sure to record the amounts found in inventory, food production, and served to children from all feeding sites. The attached worksheet is a sample form that may be used to record information.
- For each school, compare the amount of produce that was received to the amounts in inventory, in production that day, and produce already served, as reported by the site staff.
- If the total amount of produce reported does not match the amount received, contact the school to find out why too much or too little product was identified. Reasons might include the following:
- More or less produce was received than ordered.
- The school also had the same item on hand from another source (such as a local farm) that was counted in recall.
- Leftovers from the previous week were counted in recall.
- Production records were not accurate.
- Once produce has been accounted for at each school, record the ending time and calculate the total amount of time it took to conduct the mock recall exercise.
*Conduct this mock recall according to your SOP. If the SOP states that the vendor or warehouse will communicate recall information and provide product identification directly to school sites, work with your vendor or warehouse to establish mock recall procedures and documentation.
- Step 5 - Mock Recall Debrief
- Determine who should participate in the mock recall debrief. Suggested attendees include: school nutrition director, central office supervisory or training staff, manager(s), and administrative assistant(s).
- Determine whether the mock recall was completed within the timeframe identified in advance of the exercise.
- Identify weaknesses or problem areas in your mock recall exercise.
- Weaknesses might include:
- Produce was delivered in untraceable packages or containers.
- Produce was commingled with other product.
- Produce was taken out of original packages or containers and labeling information was lost.
- Unable to contact school personnel.
- School personnel were slow in responding or not responsive to requests for recalled produce information.
- School personnel were unsure of how to identify produce tracking information on packaging.
- The amount of produce received by sites did not match the amount of produce found in inventory, production, or already served.
- Identify corrective action(s) needed to improve recall procedures. Develop a plan to implement corrective action(s), including person(s) responsible and a timeframe. An example is provided in the case study.
- If necessary, revise SOPs or conduct staff training related to food recalls based on the outcomes of your mock recall.
Mock Recall Effectiveness
The effectiveness of the mock recall exercise can be measured by using a simple formula. Upon completion of the recall, calculate the effectiveness to determine if corrective action is needed.
Recall effectiveness formula
- Amount delivered
- Amount in inventory
- Amount in food production
- Amount served or consumed
% Mock Recall Effectiveness = (B+C+D) / A x 100 = %
Example
- Amount delivered 42 cases
- Amount in inventory 35 cases
- Amount in food production 4 cases
- Amount served or consumed 1 case
Formula: 35+4+1 = 40 cases / 42 cases x 100 = 95% recall effectiveness
Effectiveness should be calculated first by site, then by district. If the mock recall is less than or greater than 100% effective, identify what caused the discrepancy and determine appropriate corrective actions.
When all of the produce is not identified, the recall effectiveness will be less than 100% effective. In a real recall situation, the unaccounted for produce may already have been served or potentially could be served in the future, resulting in increased risk and possible harm.
If more produce is identified than was delivered, the recall effectiveness will be greater than 100%. Operators may think it is not a problem to identify more produce that what was recalled, but the inability to trace the actual recalled produce shows that the system is not working properly.
Both outcomes result in a loss of traceability and increased risk of serving, or consuming, recalled food in the event of an actual emergency.
Conclusion and Next Steps
Upon completion of the mock recall, the school nutrition program director, supervisors, if applicable, and other necessary staff should discuss and identify corrective action steps. After this mock recall another exercise should be planned, even if the effectiveness was 100%. Consider using different products; choose a different day of the week and a different time of day.
While this resource provides information needed to conduct a mock recall of produce received from a distributor, consider all of your produce sources, including local farms, fresh-cut processors, produce cooperatives, and school gardens. Consider conducting a mock recall of produce from each of your produce sources.